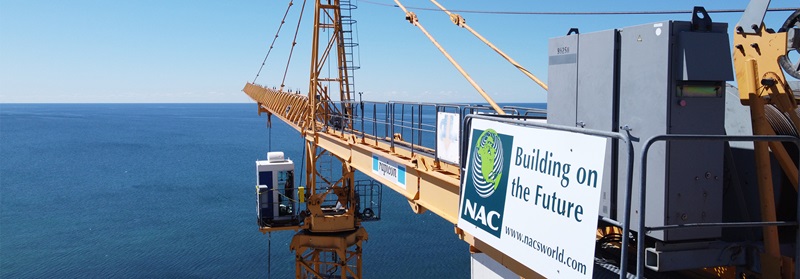
404
The page that you requested does not exist.
Our website was recently redevelopment and so the content may have been moved.
Please use the navigation above or search the site.
Our website was recently redevelopment and so the content may have been moved.
Please use the navigation above or search the site.