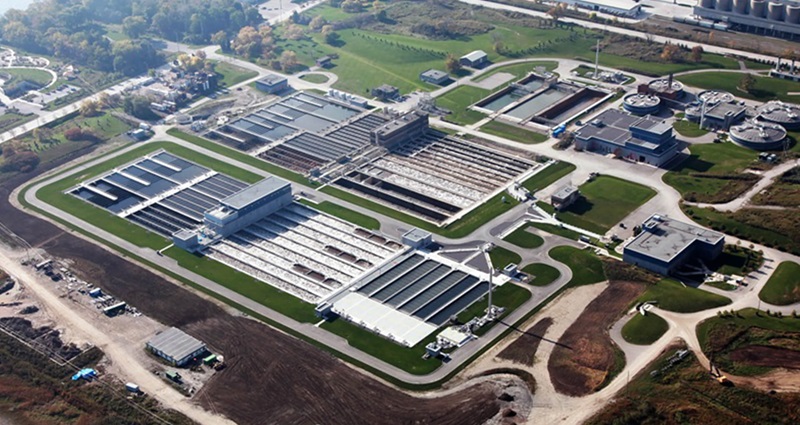
Concrete Pour Underway at $160 Million Mississauga, ON WWTP
North America Construction is now in the midst of pouring 29,000 cubic metres of concrete for nine treatment tanks at Mississauga’s Clarkson Wastewater Treatment Plant...
September 30, 2011
FEATURE | Concrete/Masonry
Concrete pour underway at $160 million Mississauga, Ontario wastewater treatment plant
DAN O’REILLY
correspondent
North America Construction is now in the midst of pouring 29,000 cubic metres of concrete for nine treatment tanks at Mississauga’s Clarkson Wastewater Treatment Plant
The concrete pour is part of an overall $160-million expansion that will increase the plant’s treatment capacity from 200 to 350 mega-litres a day. The pour started in April and will continue until July 2012.
While a massive undertaking, the preconstruction work and community relations initiatives have proved to be as equally challenging, suggest the project partners that include the contractor, owner Peel Region and its consultant, AECOM.
Located on Lakeshore Road within view of Lake Ontario, the plant has ample space for the expansion that is needed to meet rapid residential growth in Mississauga and Brampton, says William Fernandes, the region’s capital works manager for wastewater treatment.
Still, three long-defunct lagoons had to be decommissioned to make space for the tanks. “We couldn’t do this project without them (the lagoons) being removed.”
The approximately year-long removal operation carried out by another contractor consisted of dewatering — with the water retreated on site — and trucking the remaining solid waste to landfill sites, says Fernandes.
With the lagoons out of the way, excavation was able to proceed. That, however, proved to be particularly trying as large sections of the area is shale and in some spots the shale was six metres deep, says NAC project manager Mike Moylan.
“We excavated 200,000 cubic metres of earth, of which 150,000 cubic metres had to be trucked offsite.”
Ensuring mud and dirt from the trucks wouldn’t be deposited on Lakeshore Road and other area streets proved to be a challenge itself. A layer of coarse sand was applied at a separate dedicated entrance to the NAC work site.
“That didn’t work out very well. So we built a concrete pad,” says Moylan, explaining the truck tires are washed at the pad before exiting the site. Chemical dust suppressant is also sprayed on the internal roads.
A good measuring gauge on the success of those initiatives is the substantial decrease of area resident complaints about dust and dirt, says Fernandes.
Construction of the tanks is now in full progress and it involves pouring about 150 metres of concrete on a daily basis. The slabs for the tanks, which include primary and secondary aeration, and secondary final, are 450-mm-thick and the walls are between 350- and 450-mm-thick, says Moylan.
With an estimated 60 to 70 truckloads of concrete entering the plant weekly, a high degree of coordination between NAC and supplier St. Mary’s Cement is crucial, he says.
“Sometimes we schedule pours at 5:30 a.m. in the morning so their (St. Mary’s) trucks can beat the morning traffic rush. But that isn’t always possible and sometimes we have to cope with delays.”
AECOM has an on-site team of structural inspectors to ensure the concrete has the desired strength says Ignatius Ip, associate manager of wastewater engineering.
It also uses the services of material performance specialist, Davroc Consulting Engineers. The results of Davroc tests are posted on line about eight days after they are conducted, says Ip.
NAC will have an estimated workforce of 120 men on site when the project hits its peak later this fall, says Moylan, who estimates another 40 subcontractors will working there over the life of the project.
While the concrete pour will be finished next July, the project won’t be completed until June 2013. As the general contractor, NAC is also responsible for a massive amount of other work including equipment installation, mechanical/electrical connections and the construction of the blower building, says Moylan.
Originally posted on Daily Commercial News
Related delivery methods:
Related sectors:
Related services:
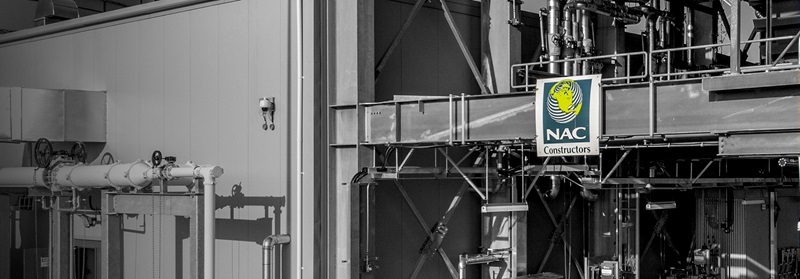
Related Projects
-
Clarkson Wastewater Treatment Plant
Mississauga,
Ontario
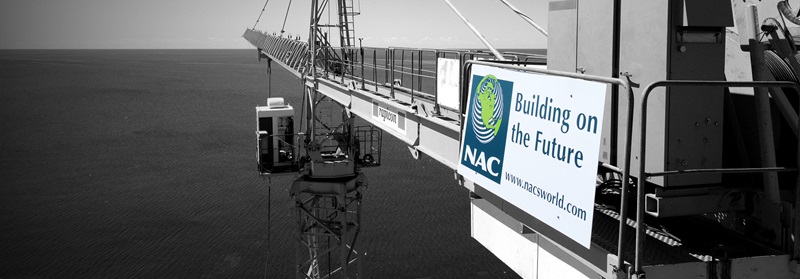